Quality assurance in gas welding: Inspector expertise essential
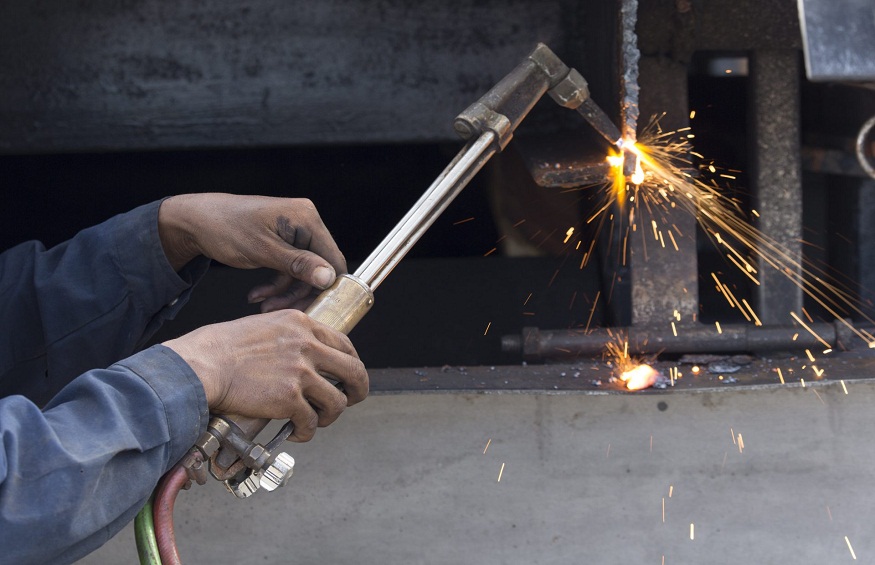
The old gas welding technique is still responsible for some part of the activity in the world of metalworking with time. Even though other welding methods are available, some plants still use gas welding to do their work steadily. However, it is critical to carry out the quality of gas welding processes ensuring its performance to the basic safety requirements through rigorous supervision with constant adherence to standards. Here this is where welding inspector credentials make the picture perfect by ensuring that every weld is designed up to the highest level of efficiency and reliability.
Understanding gas welding
The process of welding by gas and oxygen, or oxy-fuel welding, is conducive to the production of heat from a flame fueled by acetylene or propane. This is the point at which the heat of the flame causes the melting of the base metal and filler material, fusing them without any joins. This process is also quite versatile as it can join every type of metal, from steel to aluminium and similar alloys.
In the construction sector and automotive repair, working with gas welding is used. Also, gas welding is used in many others, such as plumbing and manufacturing. We can think of gas welding as the engineer’s tool for joining metal components, fixing machines, and constructing different structures. This welding approach ensures the validity of all the metalwork.
The importance of welding inspector qualifications
Gas welding offers many benefits beyond solely arising by its use however it’s crucial to create quality and safe joints as well. Incorrectly performed welding can reduce the structural performance of components to such an extent that repairs or even replacements can be quite costly while at the same time causing accidents. It is in this context inspectors step in. Weld Inspectors are trained professionals who guarantee that welded joints are fabricated using prescribed standards as well as specifications set by relevant authorities. The responsibility of the certifying inspector covers such areas as weld performance, procedure observance and safety orderliness.
Qualifications for welding inspectors
Experience requirements
Furthermore, welding inspectors will normally have to have a specific level of experience, that is, they have to have worked in the welding industry and be acquainted with it. Inspections are often more challenging because welding is a hands-on process that requires nuances to be identified. Therefore, the inspectors should understand the welding processes not only from a book but also from a practical point of view to spot possible defects and other issues during the inspections.
Knowledge of standards and codes
The most fundamental task for weld inspection officers is organizing and conducting process monitoring and maintenance operations by the national standards and regulative documents for welding operations. Submission to the standards of these norms and identification of the inconsistencies in welding techniques are among the inspectors’ essential duties.
Non-destructive testing (NDT) skills
Moreover, most welding inspectors are also NDT (Non-Destructive Testing) certified with a series of methods such as visual inspection, radiography, ultrasonic testing, and magnetic particle testing. By applying these methods, inspectors can examine the weld quality on one basis, thus, the solidity of the welded joint is not affected.
Communication and documentation skills
Communication engagingly serves welding inspectors to report on observations during the inspection in a transparent manner as the stakeholders include welders, engineers, and project managers. In principle, inspectors should monitor welding procedures and create worksheets with detailed records of all the inspections carried out at the welding stage during the quality control process.
Communication and documentation skills
Unless the inspector ensures that the communication is effective, the correct understanding of the examination findings may be blurred by stakeholders’ stakeholders, including welders, engineers, and project managers. Inspectors have to register thorough documentation of inspections that is not only filled with weld procedures, and test results but also includes deviations from standards as well.
Ensuring quality in gas welding
Quality control is an integral part of gas welding as gas welding has a significant role in ensuring structure integrity and long life. The role of welding inspectors in this context can hardly be overstated as the checkups are carried out at different phases of welding including pre-weld preparation and post-weld inspection.
Pre-weld inspection
Inspectors of weld contractors, before the commencement of welding works, check to make sure that the equipment is in proper functional condition and that all the welding processes conform to the specified requirements. This includes assessing gas cylinders for leaks, examining welding torches, regulators and surrounding areas for high levels of flammable gases, and providing oxygen via oxygen distributors.
In-process inspection
In addition to welding, inspectors must also monitor the process to observe if the correct techniques are being followed and ensure weldings are being carried out per approved procedure. This could include watching how welders do their work, keeping an eye on the welding parameters like heat input and welding speed, and performing visual (quality) inspections.
Post-weld inspection
Then, during the welding period, inspectors make a careful examination of the weld on the joined part to discover any defects or imperfections. The method may involve both visual inspection, as well as the utilization of non-destructive testing approaches like radiography or ultrasonic testing to guarantee that no damages or imperfections take place within the weld.
Quality assurance and compliance
Besides discovering individual welding seams, weld inspectors must also provide a great service in standard verification operative standards and policy compliance. These include reviewing weld procedures, implementing audits for welding processes, and making sure that welders meet essential qualification and certification requirements.
Continuous improvement of gas welding techniques
Gas welding, as a method of welding like others, is perpetually undergoing renovation in innovation. With technological advancements such as entertainment and social media, the role of cinema is becoming more and more prevalent in today’s society. An essential duty of a welding inspector is to achieve permanent licensing by remaining in close touch with the industry updates, and thus ensuring that recent innovations are being adopted in the welding operations.
Adapting to technological advancements
Tech inventions, e.g. advanced welding machines that are of high efficiency and application of robotic technologies, undoubtedly revolutionised gas welding processes. Welding inspection officers should keep themselves abreast of these developments to make sure the welding processes and material bearing the welds are consistent and compliant with the most current standards and specifications.
Conclusion
Widely applied gas welding being a vital component or the main element in the metalworking industries continues to amaze the world with its versatility, dependability and cost-effectiveness. Welding by gas is still one of the most fundamental methods used in metalworking ventures all over the world and welding inspectors, as the professionals they are, have to follow nuanced inspection protocols to ensure of quality, safety and integrity of gas welding while maintaining the top performance. Welding inspector qualifications must possess the appropriate skills to ensure the quality, safety, and integrity of gas welding processes. The gas welding inspectors perform their functions based on having the correct qualifications and being skilled enough. This helps them keep the highest standards of honesty and professionalism that enable them to make sure that the welded parts stay well-intact.