Carbon Black Filled HDPE: How Are They Transforming Materials?
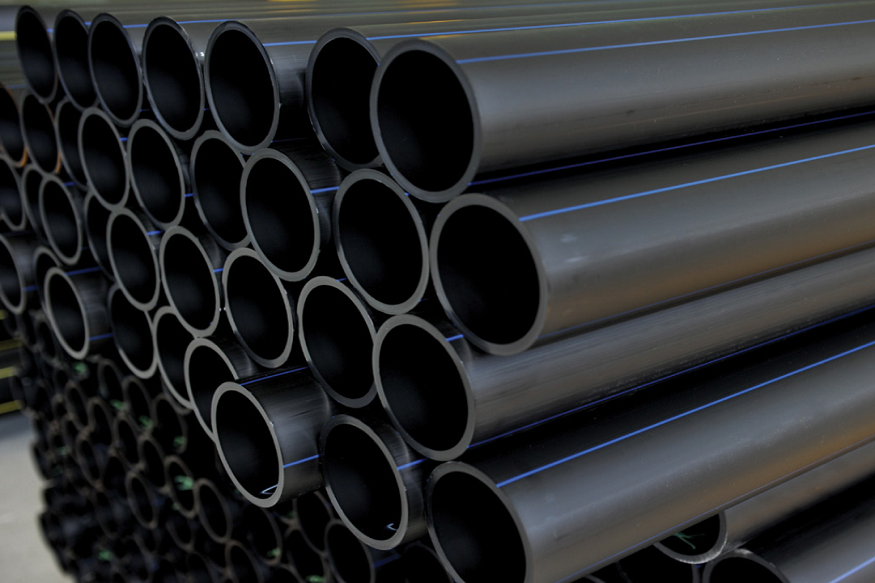
In present material technology, carbon black has become one of the maximum transforming and adaptable materials. Several distinct industries use it, which include electronics, packaging, construction, and the automobile region. Three specific developments are leading the way in transforming the performance and capabilities of materials: P-type carbon black, carbon black filled hdpe, and carbon insulating coatings. This article examines how these technologies are transforming the market for modern materials and creating new opportunities for both consumer and commercial uses.
Developments in Carbon Black Technology
Carbon Black has been utilized as a reinforcing filler and pigment for more than a century. It is a type of paracrystalline carbon that is created when heavy petroleum compounds are not completely burned. Its use has, however, been greatly increased by recent developments in material science and manufacturing techniques. With precise surface chemistries, particle sizes between 10 and 500 nanometers, and different shapes, modern carbon black particles can be manufactured to permit particular performance characteristics. Previously unreachable specialized applications have been made possible by this degree of tailoring, which has produced materials with remarkable performance profiles catered to particular industrial requirements.
High-performance engineering plastics: Carbon Black Filled HDPE
Excellent strength-to-density ratio, chemical resistance, and processability are already reasons why High-Density Polyethylene (HDPE) is prized. On the other hand, its performance qualities change dramatically when carbon black is deliberately added. Exposure research shows that HDPE filled with carbon black has up to 400% more service life in outdoor applications than unfilled alternatives, indicating significantly improved UV protection. Because carbon black can absorb damaging UV rays that would otherwise break down the polymer chains, there has been a significant improvement.
It has been demonstrated that tensile strength can rise by up to 20% and abrasion resistance can improve by 30–40% at optimal loading levels, which are usually between 2 and 4% by weight. A nanoscale reinforcing technique is used to do this, in which carbon black particles form a three-dimensional network inside the polymer matrix, better dispersing mechanical stress throughout the material. Improved creep resistance and dimensional stability under heat cycling are two of the composites’ remarkable load-bearing qualities.
The most important effect of carbon black is probably that it changes the electrical insulating properties of normal HDPE into semiconductors or even conductors, depending on the type and concentration required. HDPE now has completely new applications thanks to its electrical conductivity, ranging from electromagnetic interference (EMI) shielding parts in telecom equipment to anti-static packaging for delicate electronics. HDPE pipes filled with carbon black can now have integrated leak detection systems, something that was previously unattainable with conventional insulating plastics in the oil and gas industry.
Innovations in Electronic Materials using P-Type Carbon Black
P type carbon black is among the most important advancements in conductive carbon materials in the last few years. In contrast to common carbon black, which usually behaves like an n-type (electron-donating) semiconductor, P-type variations are designed to act as electron acceptors. Balanced charge transmission is critical in sophisticated electronic applications, where this distinction is critical. Using advanced surface modification techniques that add oxygen-containing functional groups and precisely regulated dopants to the carbon black structure, dependable P-type carbon black was developed.
Due to the availability of n-type and p-type carbon black, all-carbon p-n junctions—the essential components of semiconductor devices—have been made possible. Traditional silicon-based semiconductors are too hard or brittle for flexible electronics, thus these junctions are being used. Early uses include wearable health monitors, bending screens, and conformable solar cells that can be incorporated into textiles or curved surfaces.
P-type carbon black has helped lithium-ion battery cathodes perform much better in energy storage applications. Comparing electrodes with customized P-type carbon black to standard formulations, research published in Advanced Energy Materials showed that the former had a 45% greater capacity retention after 1000 charge cycles. Increased electron mobility inside the electrode structure and improved interfacial contact with active materials are the causes of this enhancement. The demand for stronger batteries is being driven by renewable energy storage and electric vehicles, and P-type carbon black is poised to play a crucial role in next-generation energy storage systems.
Coatings with carbon insulation: Control of Temperature reformulated
Another area where carbon black derivatives are changing the paradigms of material performance is in carbon-based insulating coatings. With the help of sophisticated carbon structures—which frequently combine carbon black with graphene, carbon nanotubes, or aerogel particles—these specialty coatings produce multipurpose surfaces with remarkable thermal management properties. In contrast to conventional insulating materials, which merely trap air to stop heat transfer, these new-generation coatings actively control thermal energy using absorption, controlled dissipation, and radiation reflection.
Carbon-based insulating coatings in building construction are meeting the increasing need for energy-efficient buildings. When applied at only 1-3 millimeter thicknesses, these coatings can drastically cut down on heating and cooling needs by 25-35% by reducing thermal transmission through walls. Concerns over electromagnetic pollution in urban areas are being addressed by these coatings, which also offer electromagnetic shielding capabilities when made with particular carbon black variations. Certain formulations use phase-change materials that are encased in carbon frameworks, allowing for dynamic temperature control that adapts to the day’s changing climatic circumstances.
Assimilation and Prospects
When combined with other materials to make use of their complementing qualities, these carbon black technologies start to have a truly revolutionary effect. Examples of dual-purpose infrastructure are HDPE pipes filled with carbon black and coated with external carbon insulation. These pipes provide thermal insulation for energy efficiency and electrical conductivity for monitoring. P-type carbon black semiconductors can also be utilized in electronic equipment that are housed in carbon black-filled polymer enclosures that offer both electromagnetic shielding and physical protection.
As we move forward, more and more research is being done on sustainable ways to produce these high-carbon materials. The carbon footprint of producing carbon black could be reduced by up to 70% by using bio-based precursors made from agricultural waste instead of petroleum-based feedstocks. Carbon black composites-specific recycling technologies are also developing, with novel methods that can recover the precious carbon materials for reuse as well as the polymer constituents.
Conclusion
P-type carbon black, carbon black-filled HDPE, and carbon insulation coating are examples of how creative ways to work with well-known materials can result in ground-breaking performance gains. Instead of being only small improvements, these technologies reflect fundamental changes in material capabilities that open up new uses and increase sustainability in a variety of industries. These carbon-based materials will play an increasingly important role in the current technological landscape as research and production grow, supporting everything from innovative electronics to sustainable transportation systems and infrastructure for renewable energy. With new developments set to push the limits of material performance and functionality, the carbon black revolution in materials science is only getting started.