The Importance of Quality Pumps in Industrial Applications: A Deep Dive into Rotary Gear Pumps and Flow Dividers
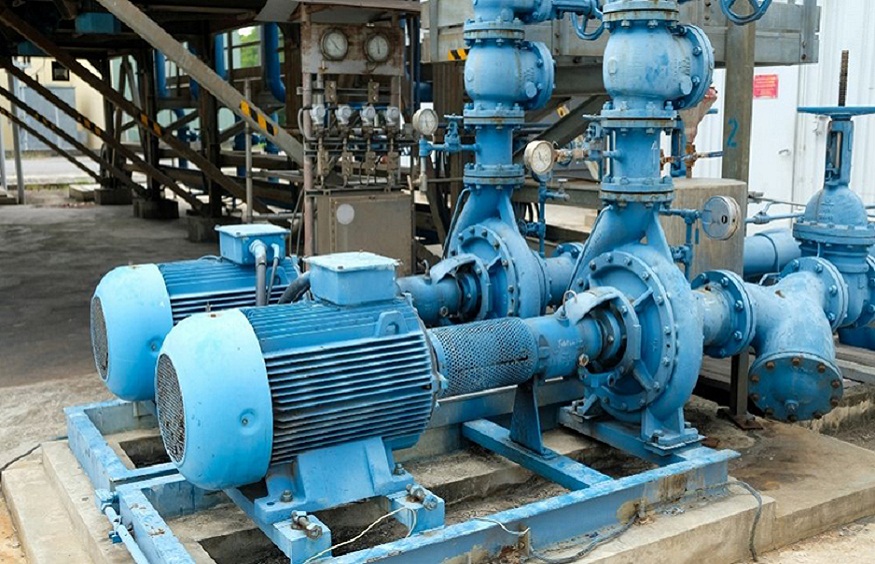
Pumps play a crucial role in a wide range of industries, from agriculture to manufacturing, chemical processing to oil and gas. Whether it’s moving fluids, ensuring the precise distribution of chemicals, or controlling hydraulic power, the performance of a pump system directly affects operational efficiency. High-quality pumps are essential to maintain productivity, reduce maintenance costs, and optimize overall performance.
Among the many types of pumps available, rotary gear pumps and flow dividers are widely used in various applications. In this article, we’ll take a closer look at the significance of investing in quality pumps, explore the advantages of rotary gear pumps, and understand the role of flow dividers in fluid control systems.
Why Investing in Quality Pumps Matters
Choosing the right pump for your business is more than just finding a product that meets your immediate needs. It’s about investing in a solution that will perform reliably over the long term, reduce operational risks, and minimize downtime. Here are some reasons why quality pumps are so important:
1. Durability and Reliability
High-quality pumps are designed and manufactured to handle the most demanding environments, whether it’s high-pressure applications, exposure to abrasive chemicals, or continuous operation in industrial settings. A well-made pump is more durable and less prone to failure, resulting in fewer repairs and lower replacement costs.
2. Energy Efficiency
Energy costs are a significant concern for industrial operations, and inefficient pumps can lead to unnecessary energy consumption. Quality pumps are engineered for optimal performance, using less power to achieve the same flow rates. This not only reduces your energy bills but also contributes to a more environmentallyfriendly operation.
3. Accurate Flow Control
Precision is key in many industrial applications, and quality pumps are designed to deliver consistent and accurate flow rates. This is especially crucial in industries such as pharmaceuticals, chemical processing, and food and beverage, where even the smallest deviations can affect product quality.
4. Lower Maintenance Costs
Regular maintenance can be time-consuming and costly. Investing in quality pumps means fewer unexpected breakdowns, lower maintenance costs, and longer equipment lifespan. This results in less downtime and more time focused on productive tasks.
Understanding Rotary Gear Pumps: A Versatile Solution
One of the most widely used types of pumps in various industries is the rotary gear pump. Known for its reliability, efficiency, and versatility, rotary gear pumps are designed to handle a wide range of fluids, including viscous liquids, chemicals, and fuels. Here’s why rotary gear pumps are a popular choice:
1. Simple and Reliable Design
Rotary gear pumps have a simple yet robust design that includes two rotating gears that mesh together. As the gears turn, they create a vacuum that draws fluid into the pump and moves it through the system. This straightforward mechanism ensures reliable performance with minimal maintenance.
2. Versatile Application
One of the greatest advantages of rotary gear pumps is their versatility. They can handle a wide variety of fluids, from low-viscosity liquids like water to thick and viscous substances like oils, syrups, and adhesives. This makes them ideal for use in industries ranging from chemical processing to food manufacturing.
3. Consistent Flow Rate
Rotary gear pumps are positive displacement pumps, meaning they deliver a consistent and accurate flow rate regardless of the fluid’s viscosity or changes in pressure. This makes them ideal for applications that require precise dosing or metering, such as chemical injection and fuel transfer.
4. High Pressure Handling
For applications that require high pressure, rotary gear pumps are an excellent choice. They are capable of generating high pressures without compromising on efficiency or performance. This makes them suitable for hydraulic systems, lubrication systems, and other demanding applications.
The Role of Flow Dividers in Industrial Systems
Flow dividers are specialized components that play a crucial role in managing the distribution of fluid within a hydraulic system. They are commonly used in applications that require precise and proportional control of flow, such as in machinery, agricultural equipment, and construction equipment. Here’s what makes flow dividers an essential part of fluid control systems:
1. Accurate Flow Distribution
Flow dividers are designed to split the flow of fluid from a single source into two or more separate paths, ensuring that each path receives a precise and proportional amount of flow. This accuracy is essential for applications that rely on synchronized movement or consistent pressure, such as in hydraulic cylinders or multi-axle vehicles.
2. Improved System Efficiency
By dividing and distributing fluid evenly, flow dividers help to optimize the efficiency of hydraulic systems. This can result in smoother operation, better control, and reduced energy consumption. In turn, this contributes to increased productivity and reduced wear and tear on equipment.
3. Pressure Compensation
Some flow dividers are equipped with pressure compensation, which allows them to maintain a consistent flow rate even when the load or pressure changes. This is particularly important in applications that involve varying workloads or fluctuating pressure conditions, such as in mobile equipment or industrial machinery.
4. Enhanced Safety
Flow dividers also play a role in enhancing the safety of hydraulic systems. By providing accurate flow control and pressure compensation, they help prevent system failures and reduce the risk of accidents. This is especially important in heavy-duty machinery and equipment that operates under high pressure.
Choosing the Right Quality Pumps for Your Application
Selecting the right pump for your specific needs is critical to the success of your operation. Here are some factors to consider when choosing quality pumps:
1. Application Requirements
The first step in selecting a pump is to evaluate the specific requirements of your application. Consider the type of fluid you need to pump, the viscosity, temperature, flow rate, and pressure conditions. Understanding these factors will help you determine whether a rotary gear pump or another type of pump is the right choice.
2. Material Compatibility
Different fluids can have different chemical properties, and it’s important to choose a pump that is compatible with the material you’ll be handling. For example, if you’re dealing with abrasive chemicals, you’ll need a pump made from corrosion-resistant materials like stainless steel or specialty alloys.
3. Energy Efficiency
Look for pumps that are designed for energy efficiency. An energy-efficient pump will reduce operating costs and minimize your environmental impact. Consider models that are designed to optimize flow rates and reduce energy consumption.
4. Maintenance and Service
Consider the maintenance requirements of the pump. Quality pumps should be easy to maintain, with readily available replacement parts and service support. Opt for a design that allows for easy access to internal components, reducing the time and effort needed for maintenance.
5. Expert Consultation
Finally, don’t hesitate to consult with experts or industry professionals when choosing a pump. They can provide valuable guidance on selecting the right model for your needs, ensuring you make an informed decision that will deliver long-lasting performance.
Conclusion: The Value of Quality Pumps in Industrial Operations
In industrial applications, pumps are the backbone of fluid management, ensuring that liquids are moved, controlled, and distributed effectively. Investing in quality pumps is essential for maintaining reliable operations, minimizing downtime, and achieving optimal efficiency. Among the many options available, rotary gear pumps stand out for their simplicity, versatility, and consistent performance, while flow dividers are critical components for accurate fluid control in hydraulic systems.
Choosing the right pump for your business requires careful consideration of your specific needs, application requirements, and long-term goals. By selecting high-quality equipment, you can improve the overall performance of your operation, reduce maintenance costs, and contribute to a safer and more efficient work environment.